Part 2: Framing a Modeling Construct to Evaluate Alternative Fleet Management Scenarios
Note: This post is the second of a three-part series that will examine the question “What is the most effective fleet management strategy based on data-driven decision making?” In part two, a modeling construct is framed to help program managers assess decision-quality trade-offs among multiple variables quickly. (Read part one and part three.)

(U.S. Air Force photos/Sue Sapp)
If effective fleet management is a complex exercise in managing competing priorities, then it is also an exercise in analytics—the scientific process of transforming data into insights for the purpose of making better decisions. As defined, this exercise must then:
Be scientifically testable, verifiable, and repeatable;
Be driven by data of sufficient availability, fidelity, and quality;
Lead to actionable insights; and
Result in high quality decisions characterized by sufficient understanding of the fleet management trade space and an accounting for necessary assumptions.
While this effort isn’t trivial, neither is it insurmountable.
A program manager’s challenge is finding the analytic “sweet spot” within analysis data requirements, complexity, flexibility, and speed. Finding that ideal position, to a large extent, hinges on the chosen analytic model’s construct. The wrong construct will yield unrealistic data requirements, as well as undue complexity, thereby limiting understanding and hindering explanation of model dynamics. Inadequate flexibility and speed will yield a model unresponsive to the program manager’s needs for forecasting, strategy development, and decision-making responsiveness to changing fleet operational, modernization, and heavy maintenance requirements.
In essence, the fundamental question is:
What are the inputs, content, and outputs of a modeling construct sufficient to inform effective fleet management data-driven decision-making?
The Modeling Construct: Thinking with the End in Mind
A good starting point for a modeling construct to evaluate alternative fleet management scenarios is the Input-Process Model-Output method of defining project boundaries and scope. The following diagram depicts the fleet management construct using that method. To “build out” the construct, one approach is to focus first on the program’s fleet management decision requirements. Fundamentally, the measures of merit (MoM) shown in the diagram provide the program manager with the minimum essential performance, schedule, and cost information necessary to explore the fleet management trade space and evaluate alternative strategies. Knowing the desired MoM helps define the required data inputs.
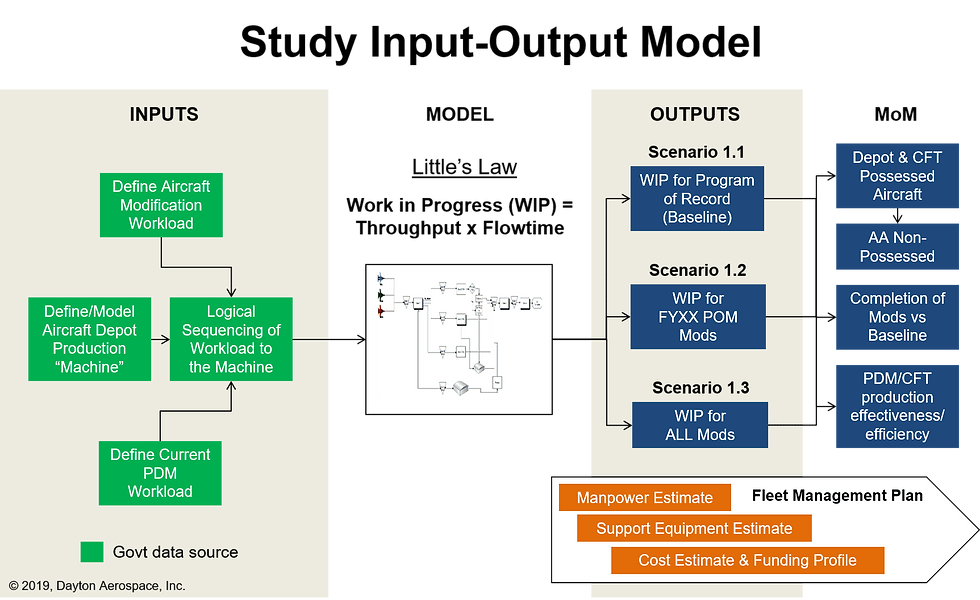
Modeling Construct Inputs: Rolling Trade Space Measures of Merit into the Vital Few
Modeling efforts live and die by the quantity, accuracy, and fidelity of the data required to feed the model. No utility exists in a discretely detailed model that lacks the commensurate data inputs. The challenge is to define the minimum level of fidelity required to meet decision requirements.
As presented in the first article of this series (here), eight measures of merit define the fleet management trade space. Detailed specification for each of these measures could make for a data collection nightmare. Instead, in the interest of model flexibility and responsiveness, a number of these measures can be rolled up into the vital few that will define depot repair/modification installation product machine capacity and throughput—planned workload and sequencing—sufficient for fleet management decision-making.
This simplification makes data collection—never an easy task—easier without sacrificing essential decision-quality measures of merit. Programmed depot maintenance (PDM) and modification installation schedules are usually readily available. Product machine construct, resourcing, etc., is more difficult to collect. However, well-structured, facilitated production estimating workshops involving production planners, engineers, and maintenance stakeholders can not only produce the needed data, but also facilitate data validation and verification.
Data produced from these workshops includes:
production flow days for each modification;
composite flow days for modifications performed in parallel or in conjunction with PDM or both;
personnel required per modification by specialty;
and required support equipment.
Model: Process Flow of the Production Machine
The fleet management decision support model itself is a structural and procedural representation of the depot and contractor field team production machines. Structurally, the model depicts the production steps, as well as the capacity (number of docks/bays, resources applied, shifts per day, etc.) within each step. Procedurally, aircraft flow through the machine, in this case, is based on Little’s Law, where Work In Progress (WIP) equals Throughput multiplied by Flowtime. Important, primary sources of this information are the facilitated, cross-functional production estimating workshops.
Modeling Construct Outputs: Turning the Dials of Budget, Schedule, and Scope
Model outputs consist of budget, schedule, and scope-related measures for each fleet management scenario alternative defined by the stakeholders. Typically, the program of record (PoR) serves as the baseline condition. Other alternatives may incorporate any combination of Program Objective Memorandum (POM) funding changes, modifications scheduled, aircraft quantities undergoing modification, and PDM cycle durations.
Model outputs lend themselves to various data visualizations useful in comparing alternatives across the model output measures of merit previously covered. Two of many possible measures of merit are shown below. The first is an example of analyzing production machine capacity (y-axis) over time (x-axis) for an alternative consisting of PDM combined with a number of modification installations.

The second data visualization compares the average number of non-possessed aircraft—a key trade space measure of merit between alternative fleet management strategies.

Dayton Aerospace Support
Dayton Aerospace is well positioned to help aircraft programs address their fleet management challenges. Our analytics and product support subject matter experts (SMEs) have successfully performed multiple analyses assessing the trade-offs between competing priorities by integrating depot maintenance and aircraft modifications to optimize aircraft availability. We have substantial experience tackling the phases of the analytics process—problem definition; business and analytic objective definition; ground rules and assumption identification; data definition; data collection and integration; analysis and results interpretation; results evaluation against objectives; and communication and deployment of recommendations. In doing so, Dayton Aerospace provides customers with data-driven decisions and the analytics necessary to perform additional inquiries. Our approach to effective fleet management utilizes the high value, authoritative sources of system data and models described in the Air Force Research Laboratory’s (AFRL) Digital Hangar as a continuum across disciplines to support effective fleet management strategies.
Part three of this series will expand fleet management strategy to the depot enterprise-level, presenting an approach to effectively address future capacity in consort with fleet management plans.

About the Author
Brian Waechter, SA, SASM, PO/PM, PfMP, LSS BB, Colonel, USAF (Ret) has over 35 years of experience as a senior acquisition, logistics, and maintenance officer; defense industry vice president and business unit leader; operations research analyst; and Lean Six Sigma Black Belt. He has helped numerous programs analyze complex fleet management challenges and develop effective fleet management strategies that successfully balance multiple program trade-offs. Read more>
Dayton Aerospace Senior Associates, Mr. Gregg Sparks and Dr. Bill Stockman, were major contributors to this article. Each has practical leadership and analytic experience in the fleet management strategy domain.